Pellet production secrets
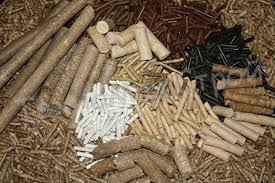
Today we are talking about full and deep processing of wood, and especially the issue of waste wood processing waste is topical. We believe that one of the best technologies for processing wood waste is pellet production. Here are a few criteria by which this technology of waste processing is superior to others:
The technology is pretty simple.
To maintain the operation of the equipment, a minimum number of personnel is required.
The cost price of production is quite small, but the return on business is high.
Possibility to process waste of various sizes. But as we already know, in order to work effectively, it is necessary to know the technology of production from A to Z. And here to the production technology is:
Raw materials, with its dimensions and humidity.
Process of operation of equipment and operating modes.
Quality of the pellets produced.
Correct packing of pellets.
At the same time on the Internet there is a rather large amount of information about the equipment of various firms. But here's how to work on such equipment, no one says which raw materials are preferable, what rates of raw material consumption, how to increase the service life of the line.
Raw materials for pellet production
The raw material for pellets is shredded wood about 1 mm in size and up to 3-4 mm in length. The advantage of pellet production is the fact that no special prepared shavings are needed here, as for example for wood-processing plants. The presence of mineral impurities and metal inclusions is not allowed in raw materials. Raw materials for the production of pellets affect the color of the finished pellets:
Black pellets are obtained from wood with the presence of bark, and the possible presence of rot by non-observance of the technology ...
Gray pellets are obtained from non-rooted wood. The photo shows that pellets have inclusions of bark. When the chip size is reduced, the inclusions may not be visible, but the pellet will have a darkish shade.
Bright pellets are obtained from quality barked wood. Light pellets have more heat, less crumbling and, accordingly, are more expensive than gray and black granules.
In addition to the color of pellets, the quality of the gluing of pellets depends on the raw materials. The fact is that the binding substance in the process of pressing pellets is natural lignin, which is contained in wood. But the content of lignin in each breed is different, and accordingly the more lignin is contained in wood the better the pellets.
Another important technological factor in the production of pellets is a wood parameter such as hardness. The fact is that the harder the wood, the greater the wear of the cutting tool, the die and the press punch.
How raw materials affect the production of pellets
Today we will consider raw materials for pellets produced from sawdust. We know that sawdust can be different and vary in breed, in size, in humidity ... Also we will consider what parameters and how they affect the production of pellets and this is especially important as it seems to us in the production of pellets by our own hands, since industrial equipment is not as sensitive as Small machine with low power.
Effect of wood species on the adhesion of pellets from sawdust
Now we turn to the main topic of this article. Pellets can be made from different types of wood, I want to tell you from which wood pellets will be produced better, what wood fits optimally, in general we will consider some criteria of raw materials for pellets ...
As everyone knows, the lignin from wood acts as a binder in the production of pellets. So, the more natural lignin in wood, the easier it is to get quality pellets from sawdust. So we need a sign for the content of lignin in wood:
Pine-27,05%.
Spruce-27.00%.
Fir-29.89%.
Beech-27.72%.
Birch-19,10%.
Aspen-21.67%.
On average, lignin is found in softwood in the range of 26-30%, in hardwood 19-28% of the total absolutely dry mass of wood. And, of course, the lower the lignin content, the more we get the cutoffs, which is a lot of energy consumption and a slight decrease in productivity.
Effect of wood hardness on pellet production
Another interesting factor in the production of pellets is the hardness of wood, the harder the wood, the more difficult it is to process it into chips, it is more difficult to compact into pellets. The power consumption is increased, the loads and, correspondingly, the tool flow (knives, matrix, rollers) are increased. I suggest you compare the hardness of some species. Wood:
Pine-260kg / cm2.
El-235 kg / cm2.
Fir-255kg / cm2.
Beech-555kg / cm2.
Birch-425kg / cm2.
The aspen is 240 kg / cm2.
Again, one cubic meter of pellets from sawdust of more dense rocks will have greater bulk density and greater heat of combustion. For example, one cubic meter of birch pellets will allocate more heat than one cubic meter of pellets from pine sawdust.
Work of the pellet production line
So, pressing is carried out due to pressing through a matrix of small sawdust. Sawdust is spilled on the matrix and then pressed into the holes by rollers rolling on the matrix. The wear of the punch rolls and the matrix is greatly influenced by a very interesting technology of launching the press
Press pellet - preparation for work
At one time when I was just beginning to study the manufacture of pellets, I did not think that this production was with so many nuances, and the technology of pellet production is so sensitive to the setting of the press. Very often you can find such a situation that pellets do not go or even a pellet press can not be started, in other words it starts, but the matrix is immediately clogged. But first about the launch of the press (provided that the matrix is already grounded).
The pellet press is started in the following order:
The main rotation motor of the punch is turned on, the chips are not fed
The primary mixture is served. Under the primary mixture, we mean the composition of oil and sawdust. The fact is that for a softer start and stop the press, as well as to increase the performance of the matrix, a mixture of pellets or sawdust with oil is fed. If you stop the pellet press with ordinary chips without oil (in the matrix of sawdust of standard humidity without oil), the compacted chips as it were attached to the walls of the matrix and then at the start it takes a very great effort to press this shaving, and this effort in many cases as a rule Not enough and the press is simply clogged, at this time there is an increased load and, correspondingly, an increased wear of the engine and the transmission mechanisms of the press. Now, in more detail about the mixture, as you understand its function a softer start of the press and less wear of the press. Specialists producing matrices and presses recommend mixing sawdust with clean diesel, automotive oil in order to reduce the frictional force between the mixture and the walls of the wear matrix, and of course the pellet with oil to be formed is then discarded, preparing a new solution for new stops and launches. Folk craftsmen or otherwise our Russian experts have adapted instead of pure and relatively expensive oil to mix shavings with cheap working off from cars, from gearboxes or other mechanisms, while the resulting pellet with oil after startup is cleaned to a stop and instead of a new mixture used many many times, Falling asleep this mixture and to stop the pellets, and to start, if necessary adding a little waste oil to the mixture. At the same time, falling asleep for the first time with the oil shavings, we get pellets with oil, then we use them at start-ups and stops of pellets with oil. The advantage of this "improvement" is the considerable savings in oil, the faster the wear of the matrix can serve as a disadvantage, since working off and with it contains a large number of metal impurities.
We are waiting for pellets to go, but we remove or pellet pellets with oil (depending on whether you use this mixture again).
After the pellet has been pushed through the matrix, the minimum supply of chips to the press is turned on, and the supply of chips with oil ceases. The chips are removed until only pellets without oil appear.
After the appearance of only clean pellets without oil, the speed of filing of sawdust in the pellet press is increased, the press is output to the designed capacity.
Why is the pellet press clogged?
If the pellet does not go, you could not press the matrix, do not spin and torture the press, you need to stop the whole system and punch or drill the holes in the matrix.
The pellet press is very often clogged with sawdust, I suggest you consider the main reasons for its clogging, when granules are not pushed through the matrix. We will assume that all technological parameters are normal:
The pressure of the punch on the matrix is normal
Moisture of chips 12-15%
The fractional composition is normal
This happens quite often when the pellet press has worked, and suddenly the load on the engine has climbed, the engine knocks out and the entire press is filled with sawdust. The operator cleans everything, prepares the matrix, starts the press and after two or three hours everything repeats again, the press stops, the operator cleans, while everything is fine, there are no comments on the technology, as it were. In fact, when they start to sort out seemingly insignificant reasons, but they are so negatively affect the work of the press:
If one of the rollers is slightly dangling or wedging - the press will not work
If the pressure of the punch is at least slightly unstable, that is, it happens that for some reason (passes the valve), the pressure is released from the punch, in which case the sensor may not immediately show a pressure drop, since at this time the pressing force of the punch decreases The matrix begins to roll a layer of sawdust. The punch rises above the matrix and the pressure remains at the same level.
An important role in optimizing the production of wood pellets is the automation and visualization of the production process.
The quality of pellets depends on:
The correct moisture content of the raw material (pellets from high humidity chips will have a larger volume than granules from shavings of low and medium humidity with the same mass)
From the fractional composition of the raw materials (the larger the shavings the more difficult it is to compact, while the finished pellet with large chips can crumble due to the restoration of the shape of the pressed chips)
From the raw material (coniferous pellets are obtained more qualitative than from the species of deciduous wood)
From the wear of the matrix and rollers (when worn, the chips are not compressed but rolled onto the die)
From the correctly adjusted gaps between the rollers and the matrix.
From the diameter of the pressed pellets (the smaller the pellet diameter, the better the quality of the pellets under the same pressing conditions)
TECHNOLOGY PELLET THINK NOW MANY MADE MORE CONCEPT.